Concept aangepast
De Chinese fabrikant van infantfood Synutra (12.000 medewerkers) heeft Carhaix-Plouguer in Bretagne gekozen als vestigingsplaats voor een greenfield mega-plant met een oppervlakte van 38.000 m² en een investering van € 170 mln. Hier wordt melk verwerkt tot droge babyvoeding, bestemd voor export naar China. De aanvoer van de benodigde 288 mln. liter melk per jaar wordt verzorgd door de 800 boeren van de regionale coöperatie Sodiaal. De bouw van deze greenfield plant is gestart in 2014 en bij de realisatie zijn in totaal tien leveranciers uit tien verschillende landen betrokken. Dinnissen Process Technology kwam in een relatief laat stadium in beeld met een afwijkend voorstel voor de dry mixing lijn. Dit bleek zoveel voordelen te hebben, dat daarvoor het concept van de plant en het ontwerp van het gebouw ingrijpend werden aangepast.
Geen producttransport
Synutra exploiteert in China al vier plants voor infant food en had al een duidelijk beeld van de menglijn, met silo’s voor het eindproduct en pneumatisch c.q. schroeftransport naar de verpakkingslijn. Dinnissen deed een voorstel voor een lean gravity mixing lijn, die optimaal gebruik maakt van de zwaartekracht, zodat producttransport via leidingen niet meer nodig is. Dat is gunstig, want elk mechanisch transport, pneumatisch of via schroeven, kan het product beschadigen. In de gravity mixing line worden alle grondstofcomponenten omhoog gebracht en van bovenaf geheel vol- automatisch gedoseerd in de menger gebracht. Het gemengde product wordt aan de onderkant uit de menger gelost en doorloopt met behulp van de zwaartekracht de diverse processtappen daaronder. Daarvoor moet dan wel de benodigde hoogte voorhanden zijn. Inmiddels heeft Dinnissen al vele lijnen volgens dit concept gebouwd. Voor dergelijke menglijnen kunnen diverse mengergroottes worden toegepast. Specifiek voor deze lijn stelde Dinnissen één menger voor met een capaciteit van 4 ton per batch, met een mengtijd van ca. 1 á 1,5 minuut.
High care big bag handling
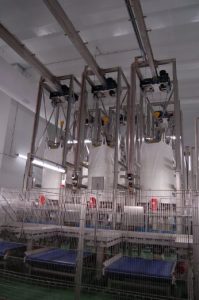
In de plant in Carhaix wordt de melkpoeder die ontstaat uit het droogproces en alle andere bulk-ingrediënten opgeslagen in bigbags in een enorm geautomatiseerd warehouse. Hiermee worden de verschillen tussen melkaanvoer en de gewenste output van de plant opgevangen. Die bigbags vormen de belangrijkste input voor de menglijn. De met Automatic Guided Vehicles (AGV’s) aangevoerde bigbags gaan op level 1, aan het begin van de menglijn, allereerst door een reinigingscabine, die de buitenzijde van de big bags reinigt met geïoniseerde lucht en UV, voordat deze de high-care ruimte ingaan. Een snelle lift, met een capaciteit van 26 units per uur, brengt deze naar level 6, op 24 m hoogte. Daar wordt de big bag overgenomen door één van de vier traverse systemen die, volledig gestuurd via in de vloer ingebouwde geleide profielen, de bigbags volledig automatisch afleveren bij het juiste van de zes losstations. Na een controlescan door de operator kan de big bag, na vrijgave door het besturingssysteem, worden ingehesen in het losstation en aangekoppeld. Gezien de hygiëne-eisen betreft het hier high-care bigbag-handling. Er zijn drie verschillende bulkingrediënten met twee big bag losstations per ingrediënt; zo is een constante aanvoer van de drie basis-ingrediënten gewaarborgd. Per batch wordt, op basis van de gewenste receptuur, de inhoud van de juiste big bags met ‘loss-in-weight’ dosering rechtstreeks toegevoerd aan de menger die er pal onder is gesitueerd.
Minors
Naast de inhoud van de bigbags zijn er ook ‘minors’, ingrediënten in kleinere volumes. Waar er in de ontwerpfase nog sprake was van drie minors, zijn er dat nu in de praktijk rond de 30, die probleemloos zijn ingepast in de besturing. Die ‘minors’ zijn gekoeld en worden in zakken aangevoerd op level 1. Daar passeert het zakgoed eerst een UV-tunnel om eventuele bacteriën te doden, waarna het de highcare-area binnenkomt. Daar wordt het verzameld in kratten, die ook met de lift naar level 6 gaan. Het traverse systeem brengt het dan naar een afzetlocatie, waar de operator het tijdelijk kan opslaan. Op een weegstation, met afzuiging, stelt de operator dan de benodigde premixes samen, die als zakgoed dan naar het stortkabinet gaan om ook aan de menger toe te voeren. In dat proces zijn een aantal keren scans nodig om te waarborgen dat de operator de juiste mix samenstelt en aan de juiste batch toevoegt.
Pegasus menger
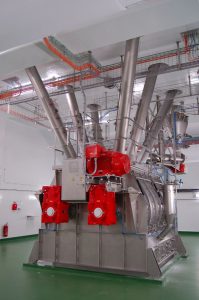
De menger, geplaatst op level 5, heeft een inhoud van maar liefst 6,5 m³, met een capaciteit van 4 ton, voor de productie van 14 ton babyvoeding per uur. De mengtijd van een complete batch is slechts 1 á 1,5 minuut. Aan weerszijden is de menger voorzien van twee grote ‘wing doors’ om periodiek een snelle droge reiniging mogelijk te maken. Deze twee-assige Pegasus paddle-mixer, een beproefd concept van Dinnissen, lost na de batch aan de onderzijde zodat er geen residu achterblijft. Het gemengde product valt dan op level 4 in een voorraadhopper waaronder een zeef is gemonteerd. Na een roterende magneet om eventuele metaaldeeltjes te verwijderen en metaaldetectie als extra controle zijn geïnstalleerd, stroomt het product verder naar beneden, naar de verpakkingslijn. Onderweg is er ook nog een mogelijkheid gecreëerd om bigbags te vullen.
Zekerheid en hygiëne
Synutra had het ontwerp van de dry-mixing line initieel gebaseerd op een opslag van het eindproduct in silo’s en pneumatisch c.q. schroeftransport naar de mengers. Dat het ontwerp tijdens de engineeringfase radicaal werd omgegooid had te maken met de significante voordelen van de Lean Gravity Mixing lijn van Dinnissen. Allereerst is er geen mechanisch transport van het eindproduct; alleen de natuurlijke zwaartekracht zorgt voor het transport door de verticale menglijn, tot in de verpakkingslijn. Daardoor is er geen gevaar voor beschadiging, ontmenging of aanhechting van het product. Het betekent ook een lager energieverbruik. Het feit dat Dinnissen de afgelopen jaren al vele mengers voor toonaangevende producenten van infant food heeft geleverd, speelde ook een rol. De complete lijn is hygiënisch ontworpen en zodanig geautomatiseerd dat deze eenvoudig kan worden bediend door 1 á 2 operators. Dinnissen fabriceerde nagenoeg alle componenten volledig zelf in de eigen productie locatie in Nederland en trad voor de hele menglijn op als turn-key leverancier en system integrator.
Bezoek Dinnissen tijdens Interpack in Düsseldorf (4 tot 10 mei 2017, Hal 4 / E26), Solids in Dortmund (10 & 11 mei 2017, Hal 6 – R55-6 pos.C) en Victam in Keulen (13 & 14 juni 2017, stand C8).