Waarom op deze manier? Nou, zoals het spreekwoord zegt: ‘’Een goed begin is het halve werk’’. Zeker met de gegevens die we ter beschikking hebben en de technologie die ons zoveel waardevol inzicht verschaft om later kostbare fouten te voorkomen. Onderstaand schema geeft aan hoe een standaard project verloopt, en welke de voorkeurspositie is van analyse van het doseringsontwerp:

Definitie
De eerste stap bij het bepalen van het geschikte ontwerp is het verzamelen van relevante informatie over de procesvereisten. Dit betekent het in kaart brengen van de eisen van de klant, specifieke lokale vereisten en dergelijke om een schets te maken van de scope van het project.
Concept design
Tijdens deze stap testen we meerdere mogelijke procesontwerpen met behulp van computermodellen en simulaties. Binnen enkele uren tijd draaien we jaren van virtuele productie door elk procesontwerp, waarbij we het optimale flexibele ontwerp definiëren op basis van de parameters in de defnitiefase.
Engineering
Onze multidisciplinaire teams ontwikkelen de complete mechatronische oplossing voor elk project. Mechanische, elektrische en software-experts werken nauw samen om ervoor te zorgen dat elk systeem wordt ontworpen volgens de huidige kwaliteits- veiligheids- en prestatie-eisen. Alle informatie moet binnen handbereik zijn voor een vlot productieproces binnen tijd en budget.
Constructie
Tijdens deze stap worden technische tekeningen omgezet in werkelijkheid. Onze machines zijn modulair opgebouwd, zodat ze gemakkelijk te vervoeren zijn en snel ter plaatse kunnen worden geïnstalleerd.
Implementatie
Tijdens het installatieproces, de inbedrijfsstelling, het testen en het optimaliseren van de systemen, worden fabrieksoperators opgeleid om ervoor te zorgen dat iedereen voorbereid is om elke dag een optimale prestatie te leveren.
Support / Care
Om ervoor te zorgen dat onze klanten een productie kunnen draaien conform het volledige potentieel van hun fabriek, blijven onze experts betrokken om continue ondersteuning te bieden; van knelpuntenanalyse van een productielijn tot het vinden van de juiste reserveonderdelen voor een geplande onderhoudsbeurt.
Waarom investeren in een goed ontwerp?
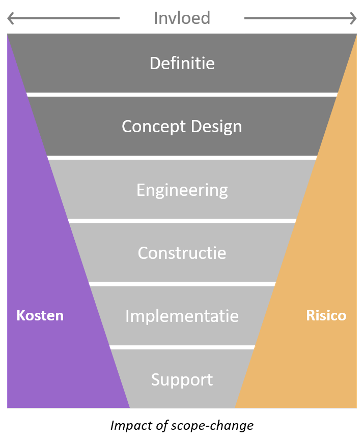
Een goede planning bespaart tijd en geld. Investeren in een goed ontwerp vereist teamwork meteen vana het begin van het project. Door het proces te bestuderen, te beginnen met de Dosing Design Analyse, worden risico’s aan het begin van het project uitgesloten, onvoorziene kosten gereduceerd en extra kosten voorkomen voor mogelijke aanpassingen die later in het ontwerp nodig zijn. Er is een direct verband met de oplopende kosten die gemoeid zijn met een wijziging naarmate je je later in het proces bevindt. Daarnaast zijn de risico’s later in het proces ook veel groter, niet alleen op budgettair vlak, maar ook wat timing en kwaliteit betreft.
Wat is nu die Dosing Design Analyse? Zo werkt het:
- Stap 1: ? Welke data hebben we nodig?
- Stap 2: Wat doen we met deze data?
- Stap 3: Welke resultaten worden er gegenereerd?
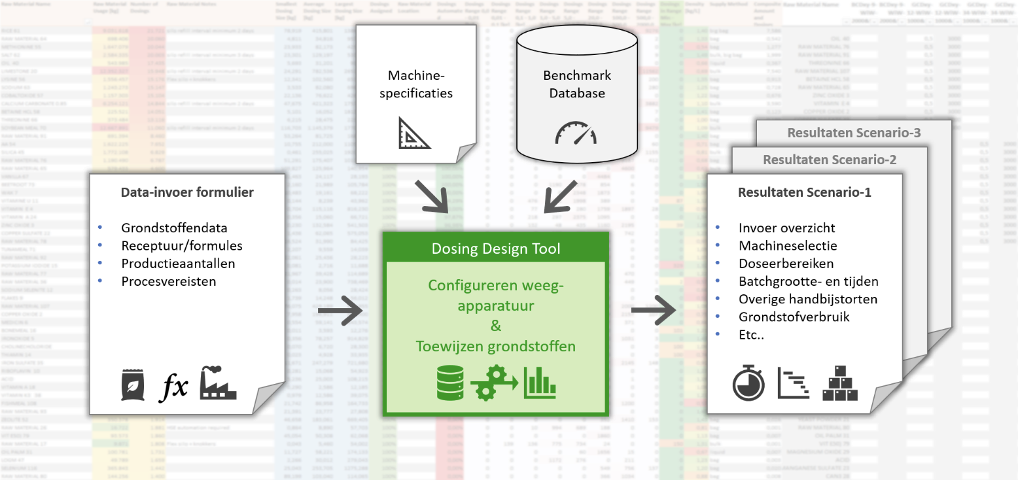
Stap 1: Welke data hebben we nodig voor de Tool?
In principe hebben we alle data nodig die betrekking hebben op uw recepten/formules, grondstoffen, productie en de huidige infrastructuur van uw fabriek.
Receptdata:
- Alle grondstoffen en recepten die gebruikt en geproduceerd worden in uw huidige fabriek en/of uw toekomstige plannen hiermee;
- Alle recepten met betreffende grondstoffen (in % of kg) die geproduceerd zullen worden in uw project.
Grondstoffendata:
- Soortelijk gewicht;
- Verpakkingsvorm bij aanlevering: bulk mechanisch of bulk pneumatisch, bigbag en/of zakgoed;
- Eventueel bekende loopeigenschappen (flowability, floodability);
- Eventuele contaminatiebeperkingen.
Productiedata
- Gewenste totale productie per jaar (KG/Y);
- Productietijden (uren/dag, dagen/week, aantal weken/jaar);
- Verwachte doeltreffendheid van de productie (meestal 70 tot 80 % bij feed, 50 tot 70 % bij premix van theoretisch maximum);
- Aantal productielijnen (mengers) en hun gedeelde bronnen;
- Per recept:
- Productiehoeveelheid per jaar;
- Maximale, gemiddelde en minimale (verwachte) batchgrootte te produceren;
- Vereiste nauwkeurigheid (hoe hoog moet de globale nauwkeurigheid van de doseringen zijn; 1, 2, 3 of 4 %));
- Minimaal aanvaardbaar aantal handbijstorten (per dag).
Bij een bestaande fabriek: gegevens van de reeds aanwezige wegers en silo’s die een rol spelen in het project:
- Silodata:
- Boven welke wegers zitten welke silo’s met welke grondstoffen?
- Wat is de doseersnelheid per weger?
- Wat is de inhoud van de silo’s?
- Wegerdata per weger:
- Doseerbereik;
- Nauwkeurigheid (uitlezing);
- Lossnelheid-tijd.
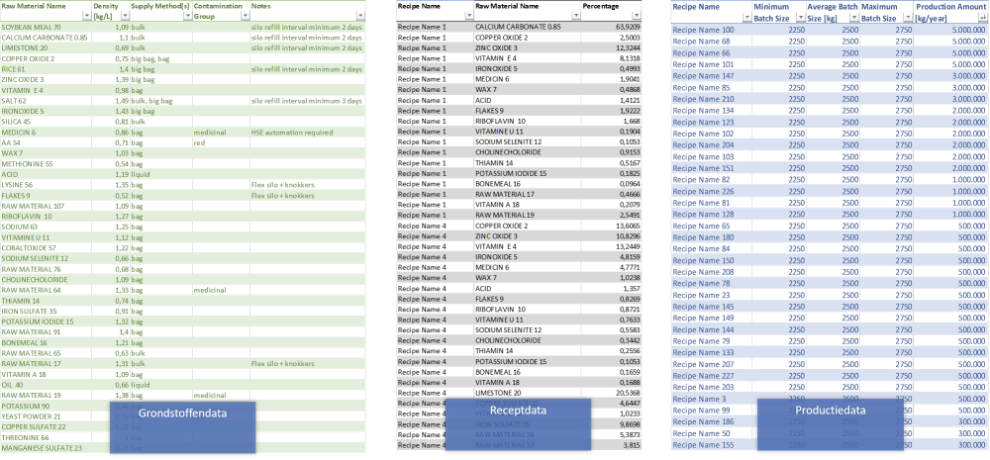
Hoe deze data aanleveren?
U ontvangt van ons een Excel-invulformulier. Uit ervaring zien we dat tegenwoordig alle bovengenoemde data vrij eenvoudig uit optimalisatie- en/of ERP-systemen te halen zijn.
Doorgaans werken wij, en onze klanten, met een vooraf ondertekende NDA-overeenkomst. Dit zorgt ervoor dat uw data en onze kennis alleen gebruikt mogen worden voor uw project, en niet onrechtmatig in verkeerde handen terechtkomt.
Stap 2: Wat doen wij met uw data?
Alle bovengenoemde data, aangevuld met onze kennis worden samengebracht in de KSE Dosing Design Tool. Hier voegen wij onze specifieke kennis van machines, ontwerpen en andere historische gegevens van vele draaiende systemen aan toe met anonieme gegevens en meten vervolgens de doseersnelheid en nauwkeurigheid in relatie tot het ontwerp en de benodigde productiestatistieken.
Loopeigenschappen van grondstoffen worden bepaald door voorgaande ervaring of door onderzoek met testapparatuur om de flowability en floodability te bepalen. We onderzoeken ook bijkomende activeringsmogelijkheden zoals het gebruikt van roerwerken, balgen, enzovoorts.
Stap 3: Welke resultaten worden er gegenereerd?
Uit de analyse worden oplossingen gegenereerd voor meerdere scenario’s zoals in te zetten weegsystemen, met bijbehorende doseerschuiven en het aantal silo’s geschikt voor uw receptuur en de gewenste productiecapaciteit. Het rapport dat voor u wordt samengesteld zal de volgende informatie bevatten:
Een samenvatting van de uitgangspunten:
- Totale productie per jaar (tonnage) en beschikbare productie uren;
- Batchtijd (dit is de tijd waarbinnen elke weger zijn doseringen moet hebben afgerond);
- Totaal aantal geproduceerde batches per jaar;
- Aantal belegde grondstoffen en resterende handbijstorten (aantal en kg).
Voorbeeld:
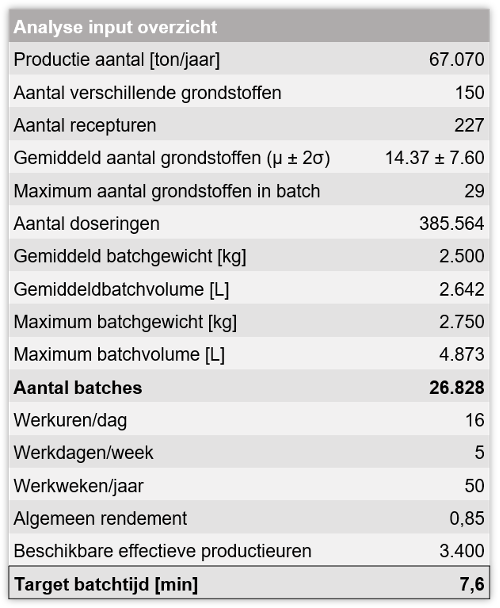
Een samenvatting van de benodigde wegers en silo’s, eventueel met meerdere combinatiemogelijkheden:
- Minimum en maximum te doseren hoeveelheid van alle grondstoffen;
- Totaal aantal doseringen per jaar per systeem, ter rechtvaardiging van de aanschaf;
- Aantal doseerposities (silo’s) per systeem, met de belegde grondstoffen;
- Batchtijd van alle recepturen;
- Percentage overschrijding van de nagestreefde batchtijd;
- Per batch:
- Kleinste, gemiddelde en maximale dosering;
- Maximale batch in gewicht en volume;
- Gemiddeld aantal doseringen;
- Eventuele extra lossingen.
- Eventuele reserves voor toekomstige uitbreiding;
- Eventueel benodigd aantal vulacties en handbijstorten.
Voorbeeld:
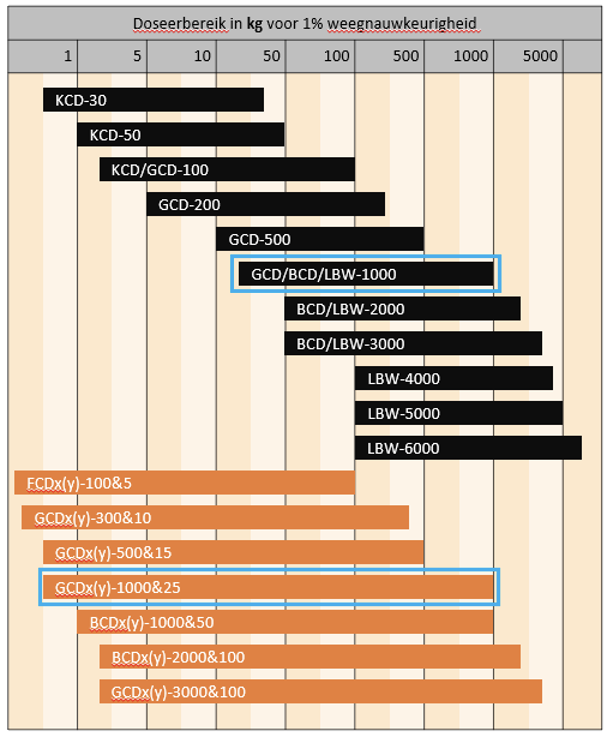
Een overzicht van de grondstoffen (silo):
- Toewijzing, welke weger;
- Aantal doseringen per jaar;
- Verbruik per week, per jaar;
- Voorstel silo-inhoud;
- Aantal vulacties, intervallen per dag;
- Maximale, gemiddelde en kleinste dosering.
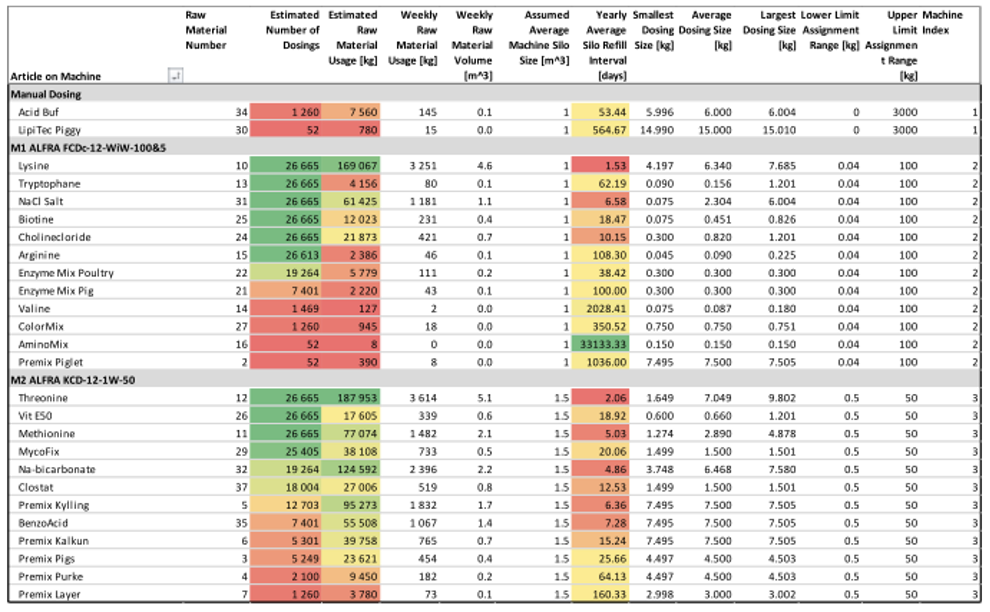
Wat is de volgende stap?
Mogelijke vervolgstappen omvatten de mechanische pre-engineering, automatisering en simulatie. Tijdens dit proces integreren we de wegers en silo’s in het ontwerp en bestuderen we het proces van de afvoer van de wegers naar de mengers en het vullen van de grondstofsilo’s. Het spreekt voor zicht dat wij altijd rekening houden met uw uitgangspunten zoals: budget, energieverbruik, contaminatie, productbehandeling en batch, zowel bij een greenfield als bij een brownfield project.
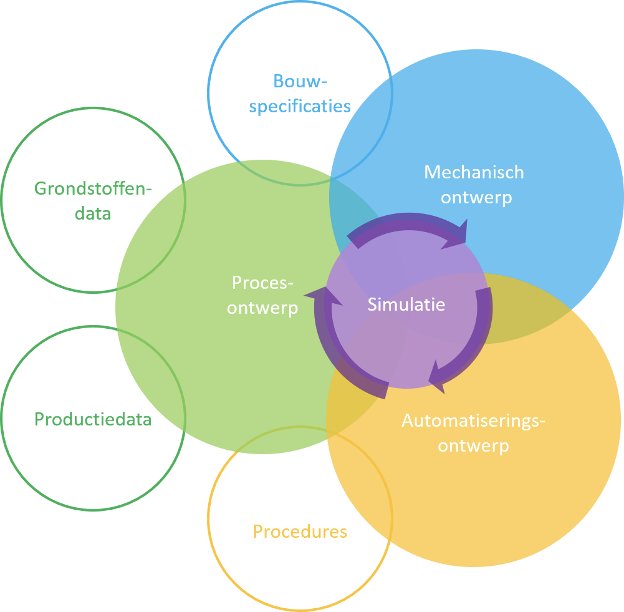