Na ongeveer vier jaar moest de band van de bijna 3,5 kilometer lange overland conveyor op een snelle en efficiënte manier worden vervangen. In plaats van de afzonderlijke delen van de band na elkaar te vervangen en hiervoor het bedrijf gedurende langere tijd stil te leggen, schakelde BEUMER Group een procedure in waarmee de nieuwe band in één keer in de installatie kan worden getrokken en de oude band eruit kan worden gehaald. Dit levert een aanzienlijke tijdwinst op voor de klant en voorkomt ongeplande systeemstoringen.
Kunnen concurreren met ‘s werelds grootste cementfabrikanten en voorbereid zijn op lucratieve bouwprojecten, is precies dat wat veel bedrijven in de bouwmaterialenindustrie voor ogen hebben, net zoals TPI Polene Public Company Ltd. Om dit te bereiken heeft de op twee na grootste cementfabrikant in Thailand installaties nodig die betrouwbaar werken en zich aanpassen aan de toenemende eisen van de markt. “In 2013 gaf TPI ons de opdracht om een complexe transportinstallatie te installeren dat kalksteen van de steengroeve naar de mengopslag transporteert”, zegt Alexander Unruh, projectmanager Transport- en laadtechniek bij BEUMER Group.
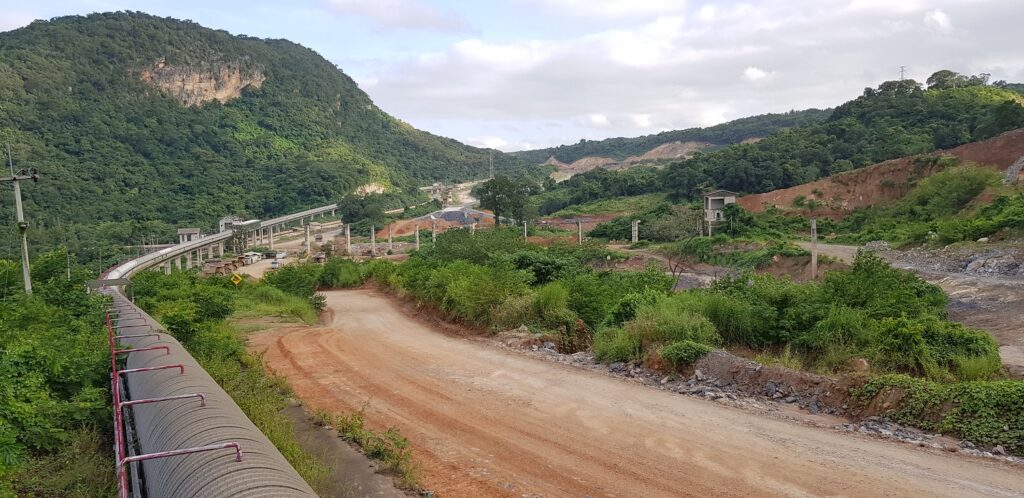
Het BEUMER-team plande een rendabel totaalsysteem bestaande uit meerdere belt conveyors. Bovendien leverde de systeemleverancier een systeembesturing (PLC), transfer stations, filterinstallaties en afscheiders voor vreemd materiaal. De installatie is ontworpen voor een transportcapaciteit van 2.200 ton per uur. De kern van de transportinstallatie voor kalksteen bestaat uit twee neerwaarts gerichte, door een generator aangedreven belt conveyors, gevolgd door een trog belt conveyor met horizontale bochten. “Het materiaal gaat van de afvoerband van de breker naar de eerste twee trog belt conveyors,” verklaart Unruh. “Vervolgens wordt het materiaal via een versnellingsband met een snelheid van vier meter per seconde overgebracht naar een overland conveyor met een asafstand van 3.464 meter. De conveyor is voorzien van verticale en horizontale bochten en bereikt een snelheid van 4,5 meter per seconde. Drie conveyors transporteren het materiaal uiteindelijk naar de mengopslag.
Om het materiaal uit de mengopslag te halen en de primaire hopper van de ruwe molens te voeden, leverde BEUMER Group extra belt conveyor systemen met een totale lengte van 989 meter. In slechts elf maanden slaagde het BEUMER-team erin om alle conveyors te bouwen en te installeren. Na de inbedrijfstellingsfase van drie maanden werden de prestatietests uitgevoerd. Vervolgens overhandigde de systeemleverancier de gehele installatie aan de klant. “Dat was in 2015, maar het project was voor ons nog niet af”, benadrukt Unruh.
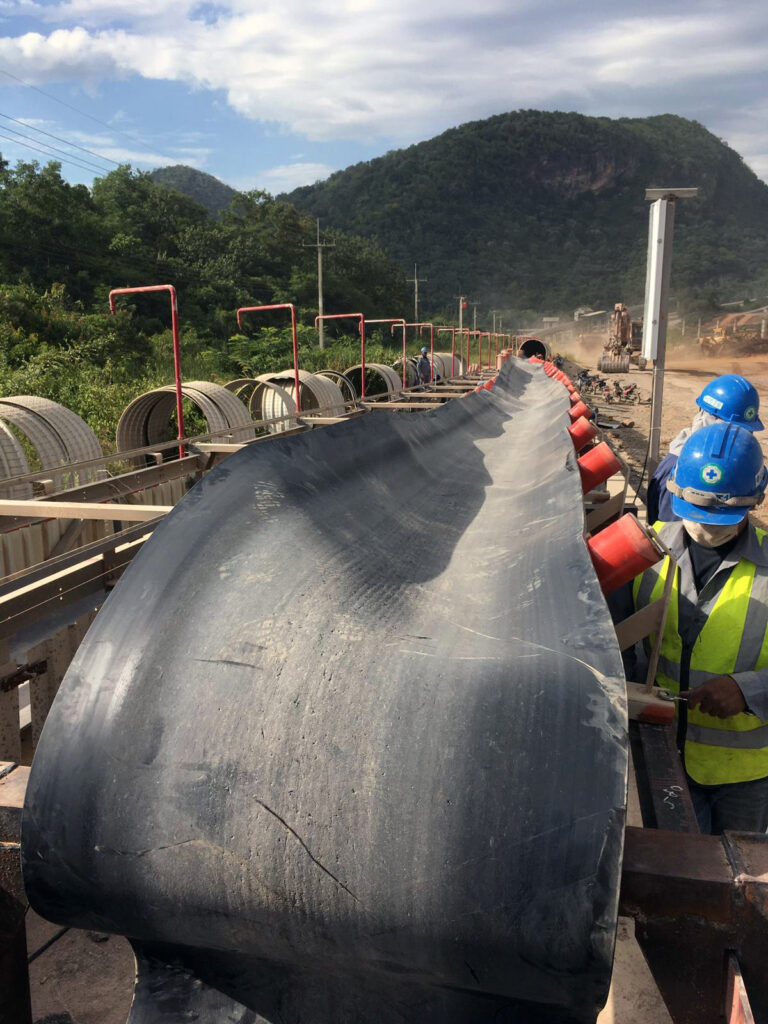
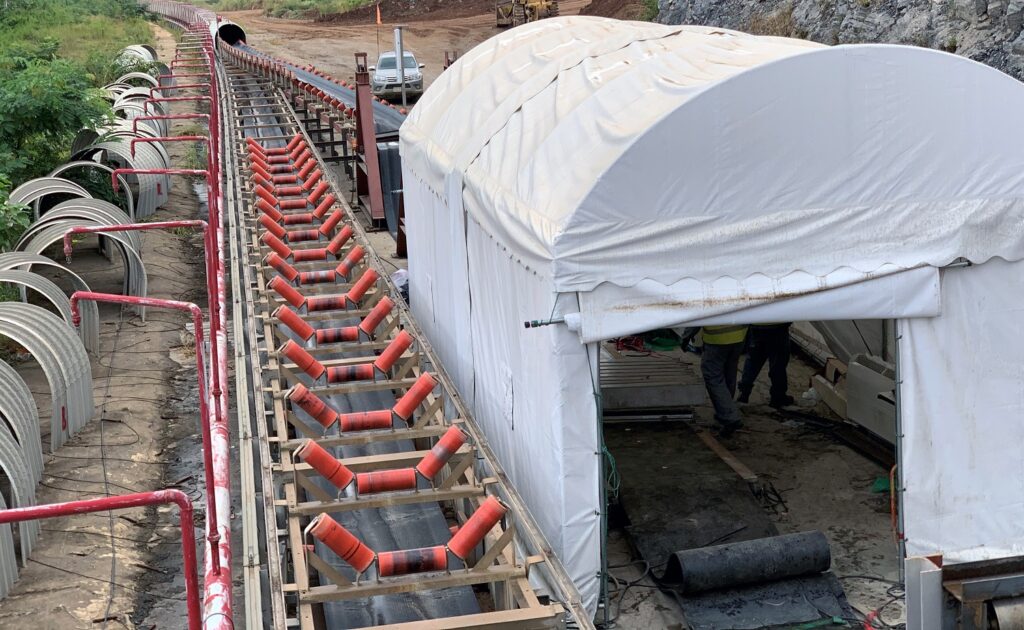
Een constant probleemloze werking
De technici van BEUMER hebben niet alleen de installatie en inbedrijfstelling begeleid en gemonitord. Bij de standaard levering hoorde ook een intensieve opleiding van het bedienings- en onderhoudspersoneel, een taak die de uitgebreide BEUMER Customer Support op zich neemt. Intussen werken wereldwijd meer dan 1.000 werknemers in dit bedrijfssegment. “Wij zijn begaan met onze klanten vanaf de eerste bespreking van het project tot het inbedrijfstellen van de installatie, maar zorgen er ook voor dat de installatie op de lange termijn betrouwbaar draait”, benadrukt BEUMER-deskundige Unruh. Na vier jaar onafgebroken in bedrijf te zijn geweest was er een hoger risico op uitval van de overland conveyor omdat de band begon te slijten.
De conventionele methode voor het vervangen van de band zou betekenen dat de servicetechnici de band moeten vervangen door elke sectie afzonderlijk te vervangen. Afhankelijk van de band kan deze bestaan uit acht tot 18 secties. “Natuurlijk neemt dit zeer veel tijd in beslag als de werknemers dit werk in één keer doen,” zegt Unruh. Tijdens de vervanging staat de volledige installatie stil. Daarom stelde de cementfabrikant voor om de afzonderlijke delen geleidelijk te vervangen. Op die manier kunnen de stilstandtijden worden ingepland zodat de workflow er zo min mogelijk onder lijdt. Maar de totale stilstandtijd van de conveyor zou nog steeds zeer hoog zijn en er was nog steeds risico op uitval. “Het vervangen van een band op een conveyor van deze lengte is altijd een groot knelpunt,” weet Unruh.
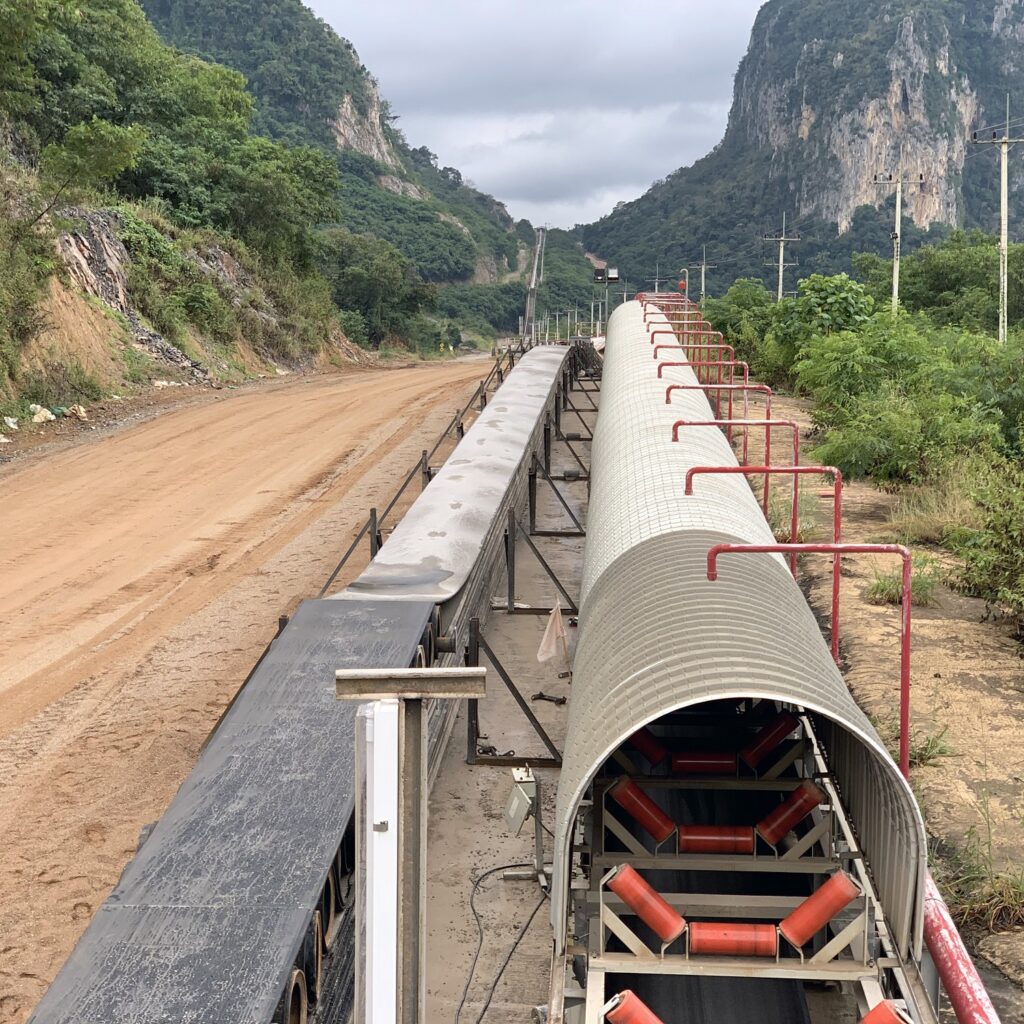
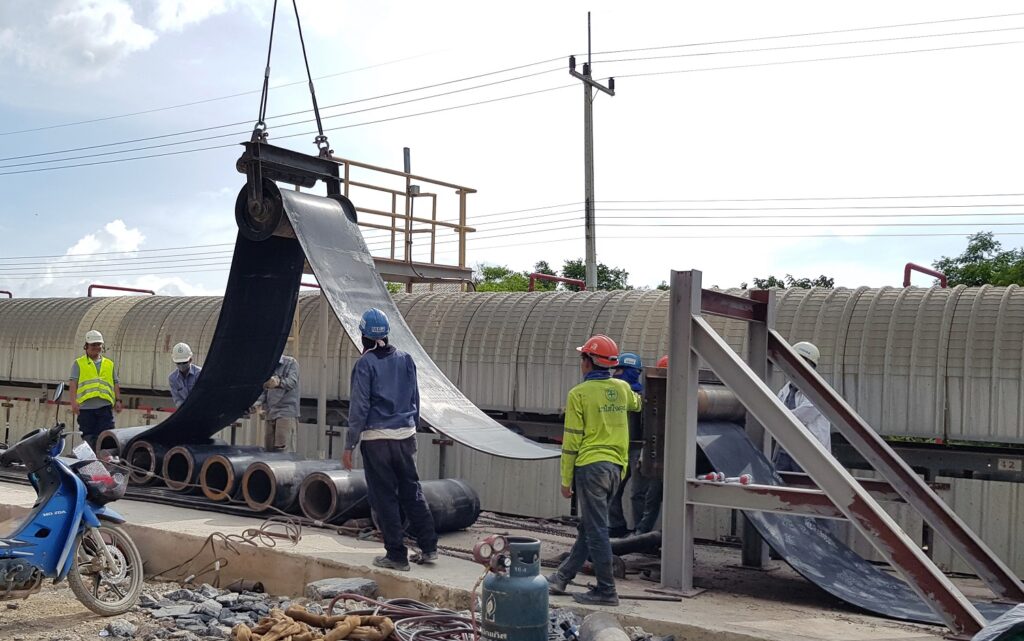
De band in één keer vervangen
Om de stilstandtijd tot een minimum te beperken, stelden de technici van BEUMER een nieuw concept voor waarmee de volledige band in één keer kan worden vervangen. “Met deze procedure monteren we de afzonderlijke delen van de band naast de transportinstallatie tot een lange band en verbinden we ze met de oude band,” legt Unruh uit. “Met behulp van de aanwezige aandrijftechniek en andere hulpmiddelen trekken we dan de nieuwe band in de installatie, terwijl we tegelijkertijd de oude eruit trekken.”
De technici van BEUMER zochten eerst op de conveyor naar een geschikte plaats om de nieuwe band te verbinden. Hierbij was het belangrijk dat deze plaats direct op de installatie lag, gemakkelijk toegankelijk was en voldoende ruimte had voor de werknemers om de band voor te bereiden. Want om de uiteinden van de banden met elkaar te verbinden, worden ze in principe gevulkaniseerd. Daarom is voldoende ruimte nodig voor de bewerking en de nodige materialen. “De delen van de band werden buiten bewaard en met een speciale folie tegen uv-stralen beschermd. De band werd in een geconditioneerde tent verbonden,” licht Unruh toe. “Waarom geconditioneerd?”, herhaald Unruh. “Omgevingsfactoren zoals het terrein, maar vooral ook het weer kunnen het vulkaniseren lastiger maken. Sneeuw, vorst, ijs of regen kunnen ervoor zorgen dat werknemers gedwongen een pauze moeten inlasssen omdat het proces niet alleen veel warmte maar ook tijd vergt. Zo zou ik bijvoorbeeld ook in India geen band vervangen tijdens de moesson.
Dankzij de voorbereidingen en hun uitgebreide ervaring kon het BEUMER-team de totale stilstandtijd voor de vervanging van de band betrouwbaar inschatten. De werkzaamheden zelf werden uitgevoerd door het servicepersoneel van de klant. Een supervisor van de bandenleverancier was ter plaatse om toezicht te houden op het werk.
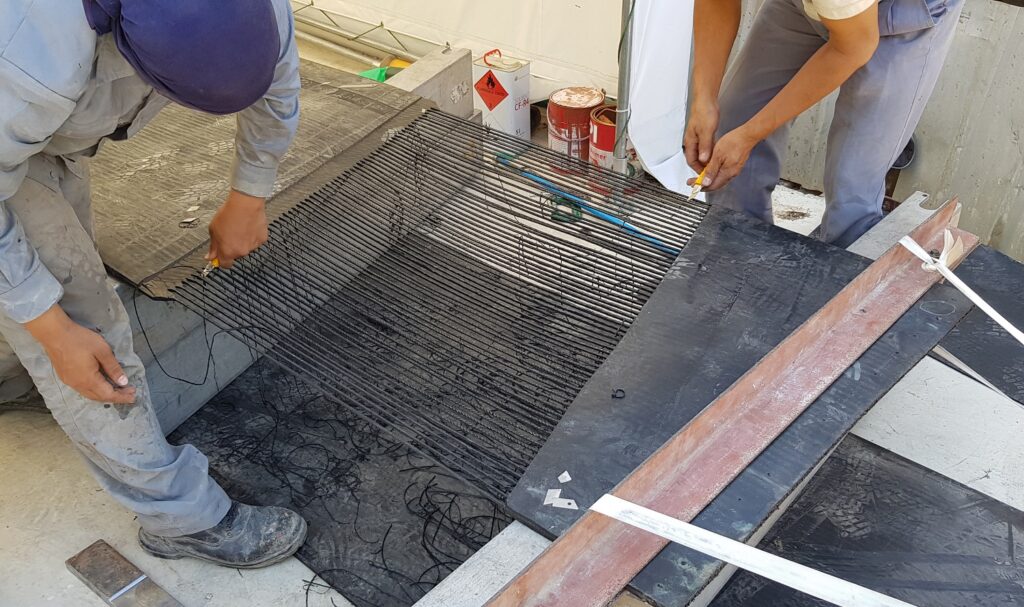
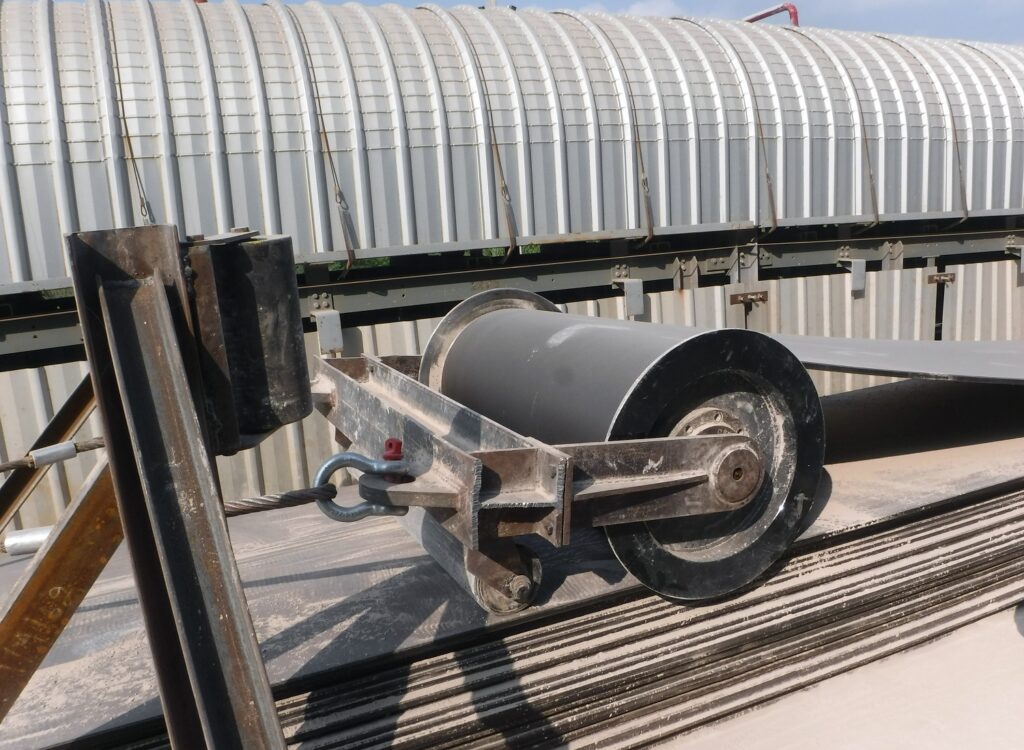
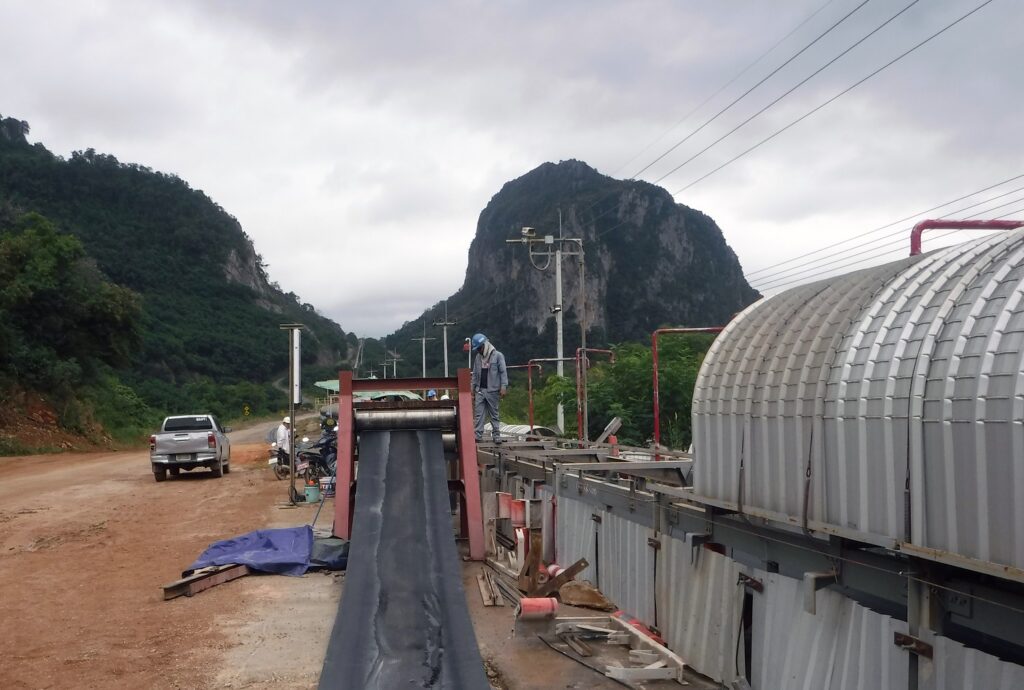
Minder stilstand, minder kosten
“De traditionele procedure mag dan wel in eerste instantie goedkoper zijn wat betreft de directe kosten”, verklaart BEUMER-deskundige Unruh. “Maar de nieuwe procedure overtuigt door de aanzienlijk lagere stilstandtijden.” Daarom is deze manier net voordeliger als je kijkt naar de totale kosten die voor de klant door een stilstand ontstaan, bijv. bij transportinstallaties met een lengte van meerdere kilometers, zoals die van TPI Polene Public Company Ltd. “En omdat we de band in één keer kunnen vervangen, geeft dit de exploitant duidelijk meer zekerheid: het risico van een ongeplande stilstand is zo goed als niet aanwezig”, aldus Unruh.