De kleine deelgemeente Retznei ligt direct aan de Mur in Stiermarken in Oostenrijk. Veel inwoners van dit gebied leven van het verbouwen van druiven, fruit, pompoenen en bonen. De belangrijkste werkgever is echter niet de landbouw, maar de cementproductie: Lafarge Zementwerke GmbH, een LafargeHolcim-onderneming met hoofdvestiging in Rapperswil-Jona in Zwitserland. “Sinds 1908 wordt er cement in Retznei geproduceerd,” zegt Franz Wratschko van Lafarge Zementwerke, die als investeringsmanager in de fabriek Retznei actief is. Destijds had de eerste exploitant van de fabriek, de Portland-cementfabriek in Ehrenhausen, volgens een oud rapport een jaarlijkse productie van 4.000 tot 4.500 wagons; vandaag de dag bedraagt het jaarlijkse productievolume ongeveer 625.000 ton. “Onze fabriek geldt als de absolute economische motor voor deze regio,” zegt Franz Wratschko.
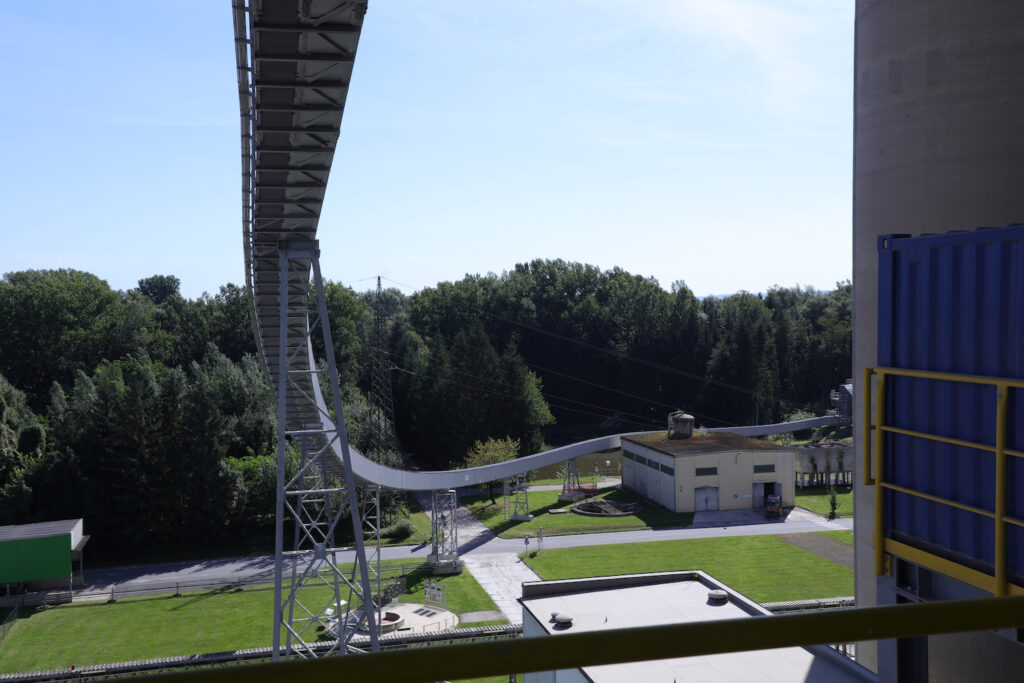
Lafarge Zementwerke hecht niet alleen veel belang aan kwalitatief hoogwaardige producten, maar ook aan een duurzame, energiezuinige en milieuvriendelijke productie. Om de uitstoot van broeikasgassen te verminderen en de productiekosten te verlagen, gebruikt het bedrijf nu steeds vaker alternatieve brandstoffen om de nieuwe calcineeroven te stoken. In plaats van kolen en olie worden er alleen voorverwerkte en geselecteerde recyclebare materialen uit de afvalverwerking in de oven gestookt. Dit is een caloriearm materiaal met een calorische waarde van zo’n 14.000 kilojoules per kilogram. Het vormt een praktisch, goedkoop en milieuvriendelijk alternatief voor conventioneel storten en verbranding. “Het thermische gebruik van deze materialen in cementfabrieken biedt nog meer voordelen,” verklaart Franz Wratschko. “Bij de temperatuur in de draaioven van zo’n 2.200 tot 2.400 graden Celsius worden organische schadelijke stoffen volledig vernietigd. Bij de verbranding blijft er geen as meer achter en worden de verbrandingsresten volledig in de cementklinker opgenomen.” De fabrikant gaf BEUMER Group de opdracht om een transportlijn te installeren die het materiaal betrouwbaar naar de calcineeroven voert met een capaciteit van 15 ton per uur.
Economisch rendabel over de hele linie
Om cementfabrikanten op het gebied van alternatieve brandstoffen en grondstoffen – in het Engels Alternative Fuels and Raw Materials (AFR) genoemd – te ondersteunen, heeft BEUMER Group met AFR Systems een eigen bedrijfsonderdeel opgericht. “Met onze knowhow en onze op maat gemaakte systemen, kunnen wij onze klanten optimaal ondersteunen,” zegt Jan Tuma, Chief Sales Officer bij BEUMER Group in Tsjechië. “We hebben niet alleen jarenlange ervaring op dit gebied, we houden ook altijd rekening met de wensen van de klant.” Zo kan de systeemaanbieder op een gebruikersspecifieke manier de hele keten van het ontvangen en lossen van de bestelwagen tot het opslaan, transporteren en doseren van de vaste brandstoffen leveren en installeren. De klant krijgt alles vanuit één bron en heeft dus maar één contactpersoon.
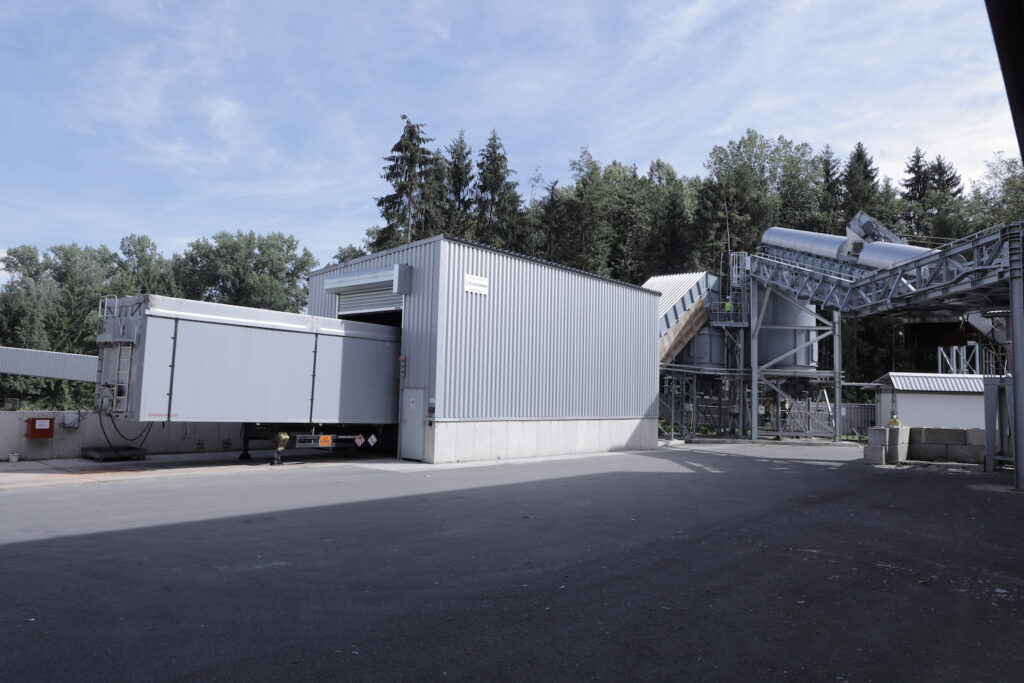
De alternatieve brandstoffen en grondstoffen dienen te voldoen aan de bijbehorende kwaliteitseisen. Zo mag er alleen verwerkt afval met een minimale calorische waarde van 22.000 kilojoules per kilogram en een overeenkomstig laag gehalte aan zware metalen worden gebruikt. Het materiaal wordt geleverd door Geocycle. De afvaldienstverlener maakt deel uit van de LafargeHolcim-groep en verwerkt bouwafval en mineraal productieafval voor de productie van klinkers in het Recycling Center van Retznei. “Het materiaal dat we ontvangen, heeft een deeltjesgrootte van 120 x 120 x 20 millimeter en een dichtheid van 100 kilogram per kubieke meter,” aldus Jan Tuma. “Het vochtgehalte bedraagt 30 procent.”
Vlotte verwerking
Geocycle levert het ovenklare materiaal in schuifvloertrailers. De hydraulisch gestuurde schuifvloer verplaatst de last naar buiten op het transportsysteem. “Alle transportsystemen en de bijbehorende apparatuur sluiten naadloos op elkaar aan en zorgen voor een continue brandstoftoevoer,” zegt Jan Tuma. “Hiertoe hebben we ons losstation BG OptiBulk geïnstalleerd.” Een chain belt conveyor met een lengte van 15 meter en een bandbreedte van 2,8 meter brengt het materiaal naar dit losstation op 6,6 meter hoogte. De BG OptiBulk is voorzien van een speciale behuizing die de omgeving beschermt tegen ontsnappend stof en het materiaal tegen omgevingsinvloeden. “Met dit station kunnen we tot 150 kubieke meter brandstof per uur lossen,” zegt de BEUMER-expert. Vanaf het losstation valt het materiaal dat per vrachtwagen wordt aangevoerd in de BG OptiFeed doseerschroefweegschaal met een bak van 20 kuub. Extra te verbranden materiaal van de afvaldienstverlener Geocycle komt via de transportinstallatie aan in een tweede BG OptiFeed met een bak van 50 kuub.
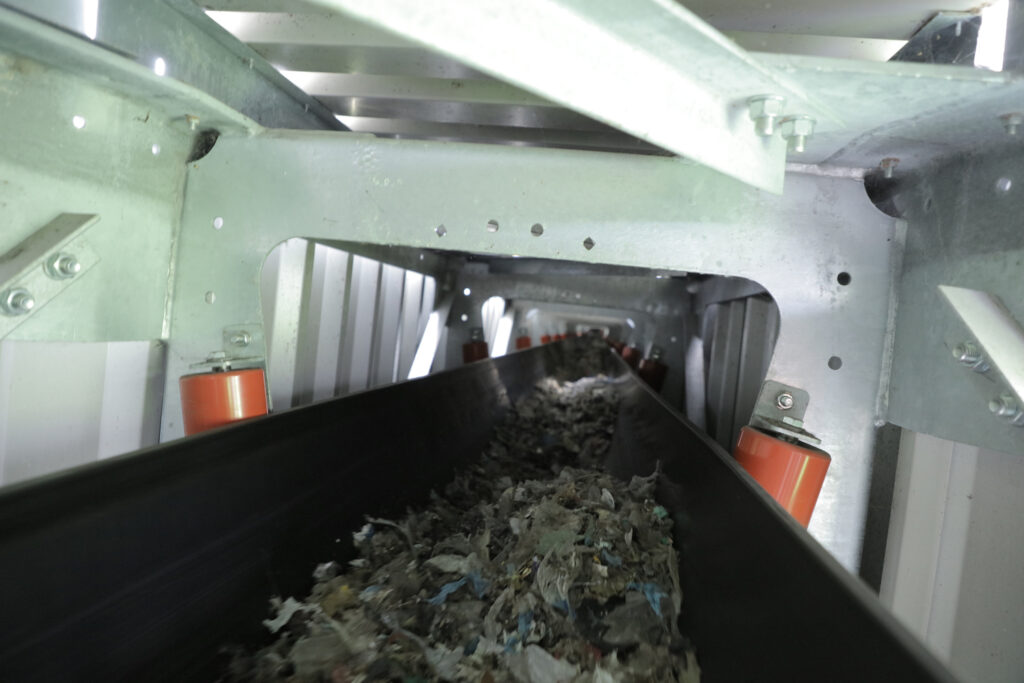
“Om het materiaal continu te kunnen doseren, hebben we voor elke materiaalstroom een van onze BG OptiFeeds geïnstalleerd,” legt Jan Tuma uit. De screw conveyor met weegcellen zijn perfect geschikt voor een grote verscheidenheid aan materialen – dus ideaal voor de continue toevoer van alternatieve brandstoffen of grondstoffen. En omdat de screw conveyors op de wegcellen staan, is altijd te zien hoeveel materiaal er daadwerkelijk wordt afgevoerd. De doorvoersnelheid naar de verdere transportelementen bedraagt maximaal 15 ton per uur. Het systeem is ontworpen voor volumegewichten van 0,08 tot 0,15 ton per kubieke meter, de regelverhouding is 1:20, de maximale toevoernauwkeurigheid tussen één en twee procent. De volledig gesloten doseerschroefweegschaal is ook beschermd tegen stof. “Zo kunnen we de volgende U-conveyor veilig met maximaal 15 ton materiaal per uur beladen,” legt Jan Tuma uit.
Betrouwbaar transport in U-vorm
De U-conveyor vormt het hart van de totale installatie. “We hebben verschillende varianten van mechanische transportsystemen geëvalueerd,” aldus de BEUMER-specialist. “Uiteindelijk hebben we voor deze transportoplossing gekozen. U-conveyors kunnen eenvoudig worden geïntegreerd en zijn ook geschikt voor lange afstanden en ruw terrein, evenals horizontale en verticale bochten. Het getransporteerde materiaal is beschermd tegen invloeden van buitenaf zoals wind, regen of sneeuw – en de omgeving tegen potentieel materiaalverlies. Deze transportoplossing is geschikt voor zowel grof als zeer fijn materiaal. De installatie in Retznei heeft een diameter van 250 millimeter, een transportlengte van 253 meter en is met een snelheid van één meter per seconde geschikt voor een hoogte van 32 meter met een maximale hellingshoek van meer dan 20 graden.
“Op het laadpunt is de U-conveyor net zo open als een conventionele belt conveyor,” zegt Jan Tuma. “Een speciale roller-configuratie brengt de band in een U-vorm.” Zo bereikt het stortgoed het uitvoerstation. Voor het openen van de band wordt een roller-configuratie gebruikt die vergelijkbaar is met die voor het vormen van de band. In vergelijking met Pipe Conveyors hebben U-conveyors aanzienlijk hogere doorvoersnelheden doordat er een smallere band wordt gebruikt.
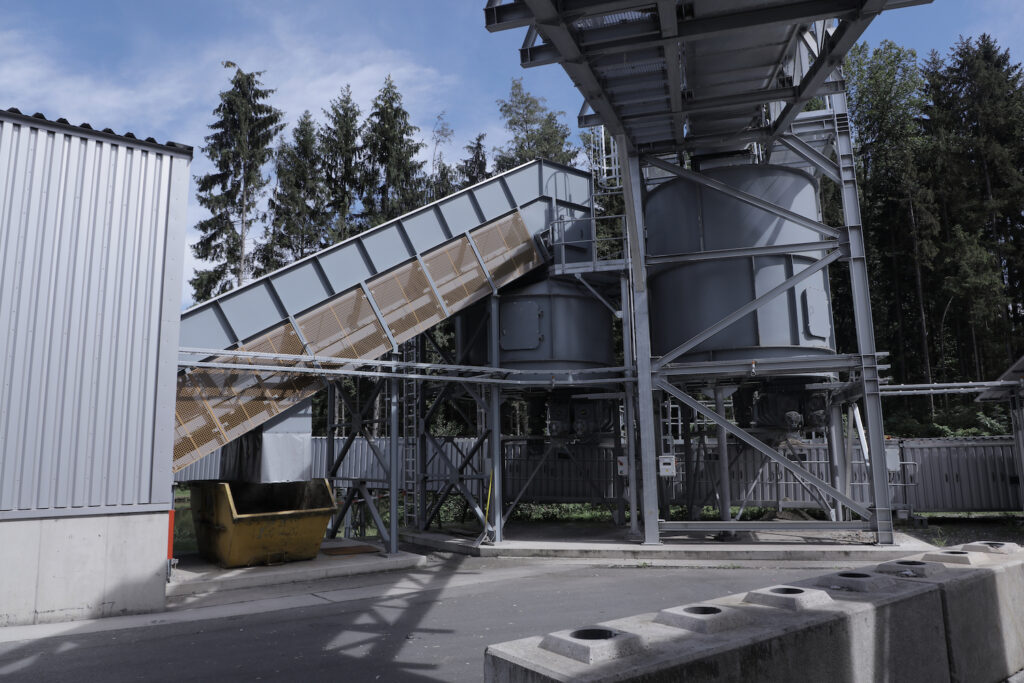
De U-conveyor transporteert het materiaal naar een dubbele discharge screw conveyor uit de BG OptiLock-typereeks. De luchtsluis van deze systeemoplossing beschermt het pyroproces tegen valse lucht van buiten die bij de verbrandingsprocessen kan ontstaan. BG OptiLock beschikt ook over weegcellen. De operator heeft altijd een overzicht van de werkelijke materiaalbelasting. De discharge screw conveyor transporteert het stortgoed continu naar een screw conveyor die de calcineeroven voedt. Omdat het materiaal kan ontbranden, heeft de systeemaanbieder alle geleverde systemen ontworpen volgens de ATEX-richtlijn voor zones 21 en 22.
“We zijn zeer tevreden met dit complete systeem,” resumeert Franz Wratschko van Lafarge Zementwerke GmbH. “De transportsystemen en de bijbehorende apparatuur sluiten naadloos op elkaar aan om een constante brandstoftoevoer te garanderen.” BEUMER Group kon aantonen een uitgebreide expertise in huis te hebben voor het omgaan met alternatieve brandstoffen in de cementindustrie en kan klanten efficiënt als partner ondersteunen, en dat op zeer korte termijn: het contract voor dit project werd in mei 2018 getekend en de installatie is in januari 2019 in gebruik genomen.